CNC machining is the most currently used for manufacturing products. The reason is its precision, consistent quality, and efficiency. Machining services are cost-effective compared to other modern methods like 3D printing. Yet, we see that the cost of CNC machining has been rising over the years.
This article addresses the rising costs associated with CNC machining. We will pinpoint the circumstances that escalate these expenses and dissect the core factors driving up CNC machining costs.
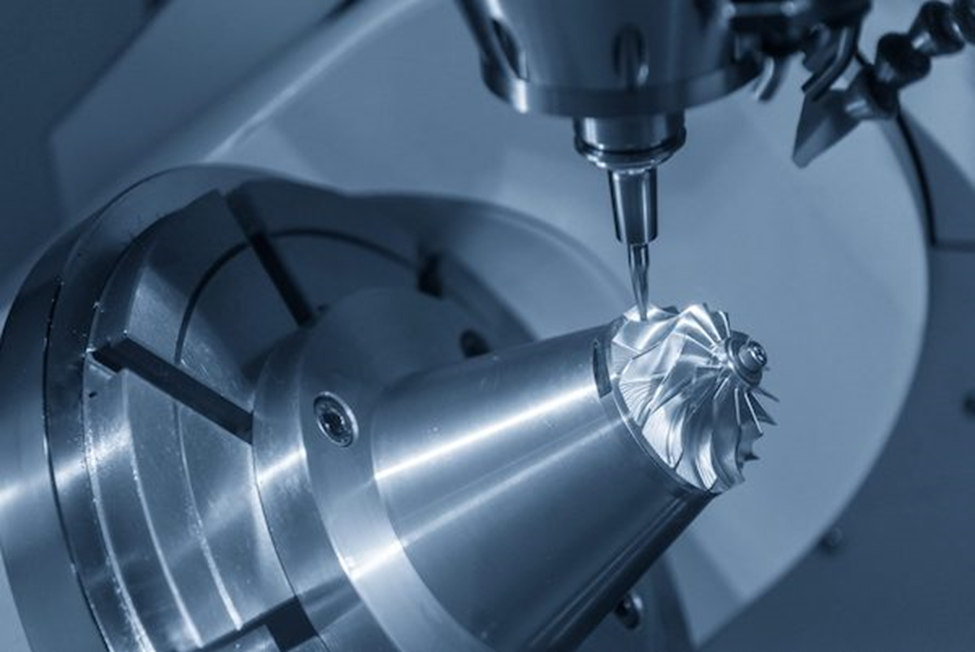
Complexity of Modern Machining Processes
As we shift from simple geometries to intricate ones, the price follows the same trend. For simple drilling or plain shapes, the cost is nominal compared to modern methods. But when you add more intricacies to the geometry like deep pockets, very sharp corners, thin walls, and non-standard. It becomes more challenging to create these parts with the existing setup.
Most CNC tool bits are cylindrical. They inherently create rounded corners inside the pockets. In most, when cases, when design requirements are flexible, this wouldn’t cause a problem. But for achieving sharp edges, with least tolerance, you’ve to move to advance process like EDM (Electric discharge machining). EDM is relatively a slower process and requires more electrical power.
Similarly, for deep pockets or holes other than standard ones, custom tool bits or attachments are needed. They are not only expensive but also have a longer lead time.
Programming also influences the cost of CNC machining. Complex geometries, one containing a range of non-standard shapes, require more sophisticated programming. This means you’ll need to hire experienced programmers to handle the job. Also, such a job would increase the overall production time.
High-Quality Material Costs
The raw material is the starting product in any machining process. If you start with high-cost material, it is obvious the end finished product will have a high cost. In some cases, the nature of the job requires certain materials. In those cases, reducing costs is quite challenging and unavoidable (mostly).

But, in instances, where you have a choice, you need to choose cost-effective and durable materials. Select material purely based on that certain use case, instead of choosing a premium material, which may exceed ample requirements. For instance, although stainless steel 316 is more expensive due to its superior corrosion resistance, stainless steel 304 might suffice for applications where such high resistance isn’t necessary.
The type and strength of the material also influence machining ease, time, and consequently, cost. Softer materials, like aluminum alloys, are more manageable and can be machined faster, reducing time and expense. In contrast, harder materials (like stainless steel) are more difficult to machine They require more robust and costly machining tools and cause more tool wear and damage.
Operational and Maintenance Expenses
Buying a CNC machine itself is a huge investment. Then, there’s an operational and maintenance cost associated with each machine. Keep in view electrical consumptions, tool costs, attachments, lubricants, labor costs, regular maintenance costs, and unplanned downtime.
We see a range of CNC machines in the market. The cost of each machine varies based on the nature of the process and the job, it can perform. Desktop CNC machines are the cheapest, available for under $5,000. CNC milling machines are available in the range of $15,000 to 50,000. CNC lathes can cost up to $45,000. 5-axis CNC machines cost the most; their prices can be as high as $250,000.
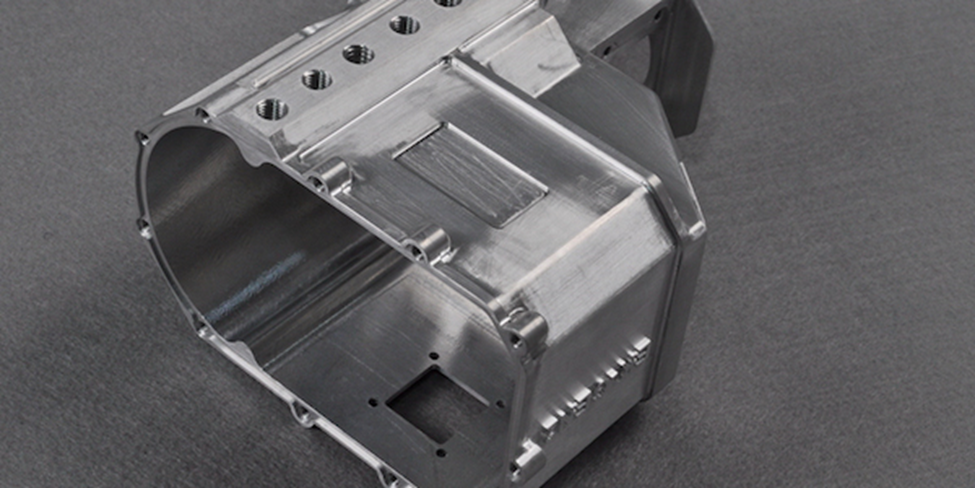
The operational costs of these machines also align with their initial cost. Higher-end machines often incur greater operational expenses. The exact operational cost is quite difficult to state as multiple variables are involved: materials, labor, and electricity – the rates of each differ based on your locality. However, one thing can stated for sure; the correlation between machining time and cost. More machining time means more power usage, more labor hours, and hence more cost.
Regular maintenance is essential for optimal machine performance, but it also means the machine is not operational during those periods. This downtime contributes to indirect costs, as it affects overall production efficiency and output.
Evolution of CNC Tools and Attachments
The tools used for CNC machining do come at a price. The standard tools are available at nominal rates. On average, a CNC drill bit costs around $2. Whereas, a CNC end mill cutter is available for under $10. These prices can vary subject to the size and tool specifications.
However, the prices rise significantly when you switch to more advanced custom tools. For instance, if you have to create a hole or a design element that deviates from standard sizes, you need custom-made cutting tools. These tools are considerably more expensive due to their specialized manufacturing process.
Furthermore, operations requiring multiple tools for a single geometry also drive up costs. A part that requires drilling, milling, and finishing with different tools will take longer to produce and involve more tool changes. This escalates both tool wear and labor costs.
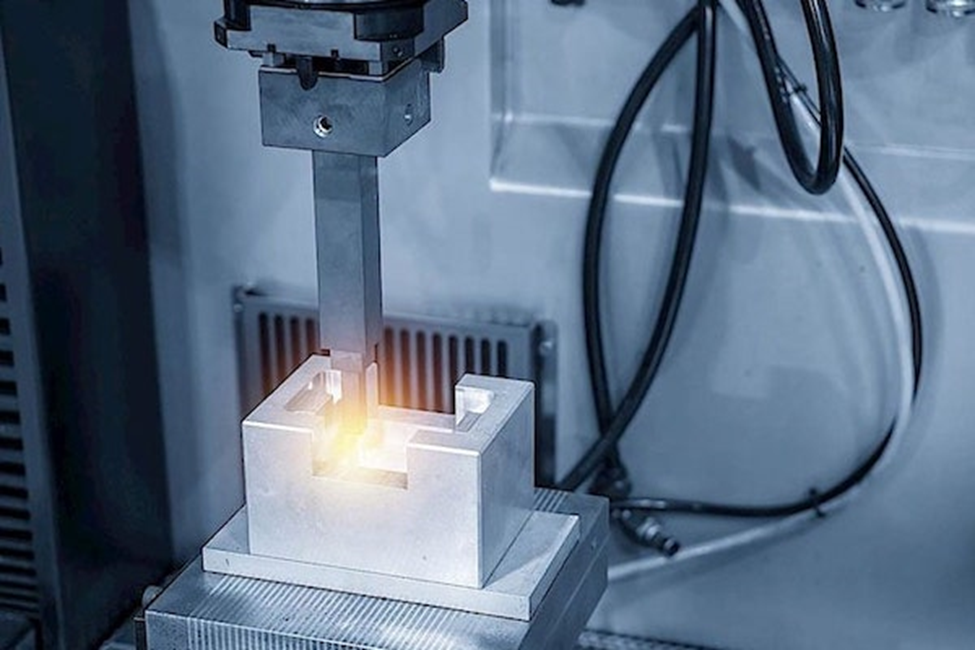
Tool wear is another critical factor. CNC machine tools are subject to wear and tear, especially when working with harder materials. This wear means tools need to be replaced more frequently, adding to the cost. In some cases, a single job may require several tools due to wear, particularly in high-volume production.
Large parts require special fixtures for stable machining, which increases the setup time and the risk of errors during machining. For example, machining a large aerospace component might need custom jigs to hold it in place securely. This is both time-consuming and costly.
Conclusion
CNC machining is often considered a cheaper solution for bulk production. However, the process cost may rise due to complex designs, the use of high-quality materials, and the use of custom tools. These costs are exclusive to capital investment and regular maintenance.
In certain scenarios, these factors are inevitable and essential for the job. However, in many instances, slight variations in design or the selection of more cost-effective materials can significantly reduce the overall cost of CNC machining.